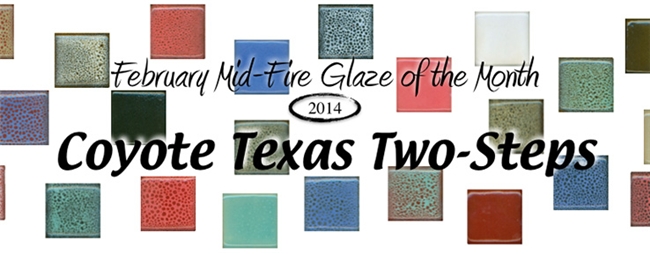
Oil spot glazes at cone 10 provide some of the most striking and unique finishes in ceramics. Now, Coyote Texas Two Step glazes provide the same sought-after effect at cone 6, in a breathtaking variety of color combinations. These food safe glazes work as a two part system, with the top coat pulling away to reveal brilliant spots of the glaze beneath. There are currently three Step One Undercoats (140-142) and five Step Two Overcoats (150-154) available.
To use the Texas Two Step glazes, simply apply a Step One Undercoat to bisque ware (two or three coats brushing, one coat dipped) and wait for it to dry completely. Then, cover all or part of the first color with a Step Two Overcoat. When the piece is fired to cone 6 in an electric kiln, the glazes will interact, creating a phenomenal oil spot effect. Varying the thickness of the glazes during application will have a dramatic effect on the finished piece, as the thicker the glazes get, the larger the spots they create will be. We found the optimum thickness to be two coats of the Step One Undercoat and three coats of Step Two Overcoat, but you may prefer thicker or thinner applications for different effects. Try experimenting!
Spots become noticeably larger and less regular after each new coat of glaze. You will need at least one Step One Undercoat and one Step Two Overcoat, used together, to get the oil spot effects.
Basic Glazing Instructions
First you want to apply wax resist to the foot of your pot (where you don't want any glaze). When you dip your pot in bucket of glaze, the glaze won't stick where you have waxed. The glazes become molten glass in the kiln, so if there is any glaze on the bottom, your pot will stick to the shelf. This will wreck your pot and your kiln shelves! Paint a thin coat of wax on the bottom, as well as up the sides at least ¼ inch. All glazes move a little in the firing, and some are quite runny. Always leave enough room for your glaze to flow some without sticking to the kiln shelf. Until you are familiar with a particular glaze, it is better to leave some extra room.
- Use a thin coat of wax. It works better and dries faster.
- Let the wax dry for at least 15 or 20 minutes before dipping a pot in glaze.
- Use an old cruddy brush, they are never the same after using for wax.
- Clean your wax brush in warm water with a drop or two of dishwashing soap.
- Be careful not to get the wax where you don't want it, i.e. waxy fingerprints.
- Before you glaze your work, you should quickly rinse it under cold water.
- Thoroughly mix the glaze just before you use it.
Dipping
To coat the whole piece in a single glaze, the easiest technique is to pick it up with a pair of glaze tongs, dip it in, count to three and pull it out. Make sure to empty it as you withdraw it. If you pull a bowl out still full of glaze it will weigh so much that the tongs will break through. Hold it upside down over the bucket to drain the excess glaze. There will probably be some glaze sticking to the waxed areas; wipe off what you can while you are holding it with the tongs. Set the piece down and let it dry. After it is dry enough to handle, turn it over and sponge off any glaze still remaining on the bottom. The foot must be perfectly clean before it can go in a kiln.
Brushing
For brushing, most glazes need 2 to 3 coats. It is easier to get even coverage if you brush the first coat side to side, then the next coat up and down.
Firing
These glazes work best when fired between cone 5 and 6 (Orton Standard or Self-Supporting Cones, used as a witness cone placed on the kiln shelf during firing). If you use a kiln sitter you usually have to use a cone six in the sitter to achieve a good cone 5. For automatic kilns, we fire to cone 5 (fast) with a 15 minute hold. Every kiln is different, so you may have to fine tune your firing to achieve the best results.